写真・文=澤村 徹
前回、Mマウント版Kistar 40mm F2.4の設計図を紹介した。クセ玉Kistar 40mm F2.4を、距離計連動するMマウントでリリースしようというプロジェクトだ。いよいよこのレンズの試作がスタートし、鏡胴パーツの製造現場を取材させてもらうことができた。Kistarシリーズが生まれる現場を見ていこう。
Kistarシリーズは木下光学研究所が製造するレンズだが、鏡胴パーツの製作は関口製作所という会社が担っている。設計は木下光学研究所がすべて行い、レンズの製作は木下光学研究所、鏡胴パーツの製作は関口製作所が担当する。そしてすべての部品がそろったら、木下光学研究所が組み立てを行う。正真正銘のメイド・イン・ジャパンというわけだ。
今回、関口製作所で見せてもらったのはマウントパーツの製作だ。MマウントのパーツというとLMリングを想起しがちだが、そうではない。外側はMマウントのバヨネットで、内側に内径リードネジを加工する。さらに外周部分にはローレットも施すという手の込んだパーツだ。これを5軸マシニングセンタで削り出していく。
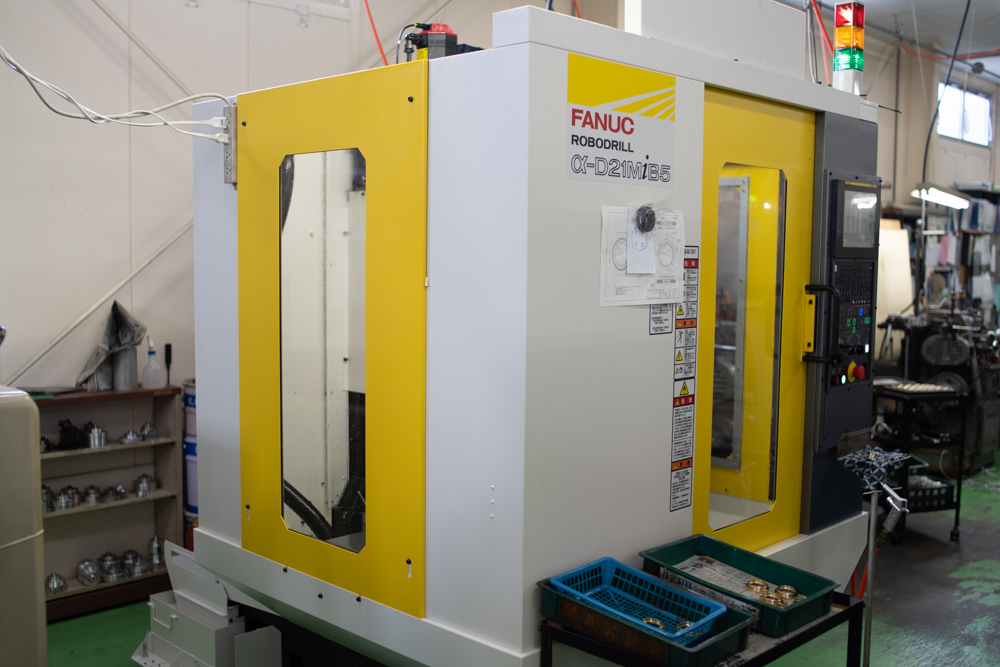
これが5軸マシニングセンタだ。パーツの大きさにもよるが、30~60分ほどかけてひとつのパーツを削り出す。
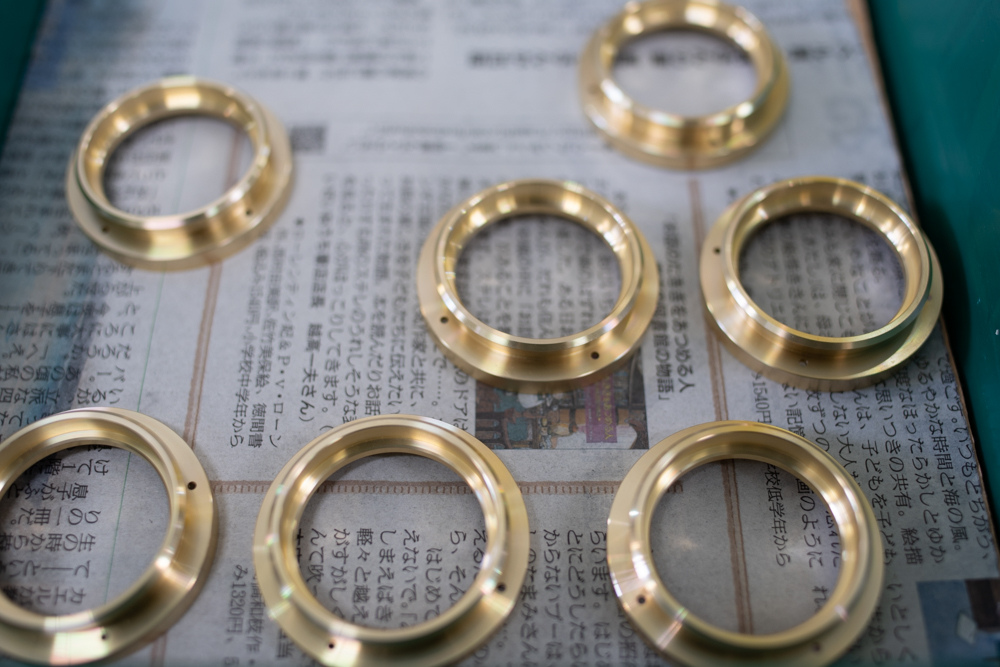
マウントパーツの元となる真鍮材だ。ざっくりとマウント形状に荒削りしてある。
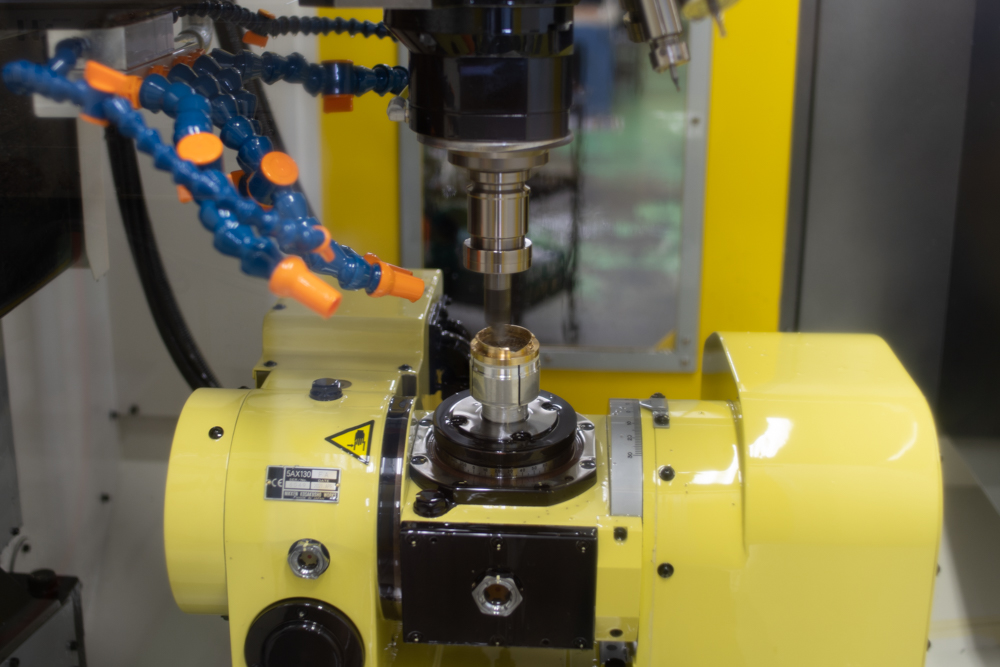
5軸マシニングセンタで削り出しているところ。中央の台座に真鍮パーツを取り付け、エンドミルで削り出していく。
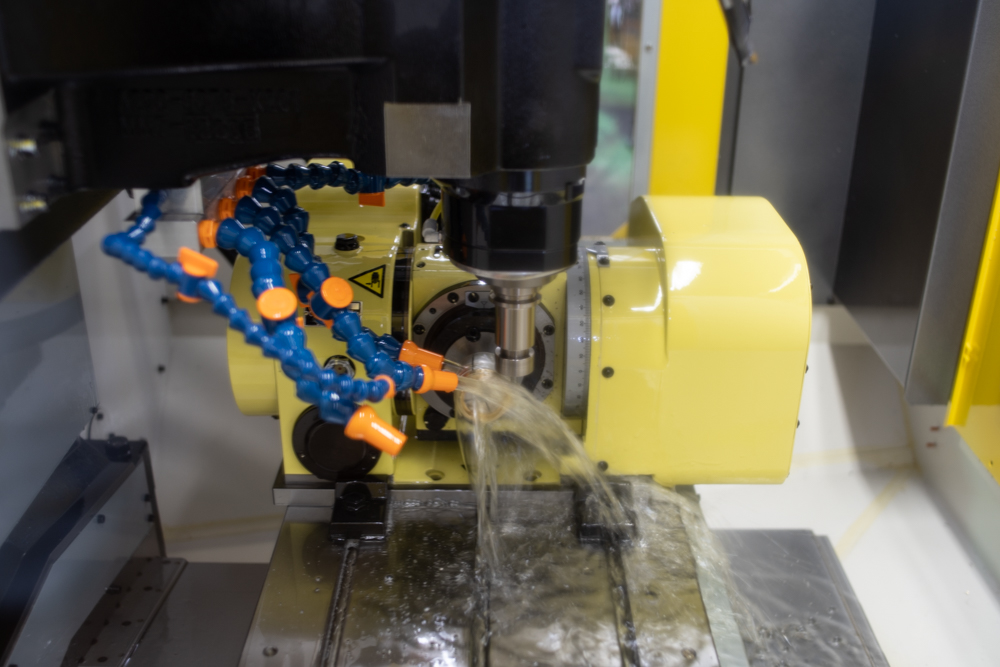
先の写真とくらべ、台座が横向きになっているのがわかるだろう。このように加工面を移動しながら削り出ししていくのだ。
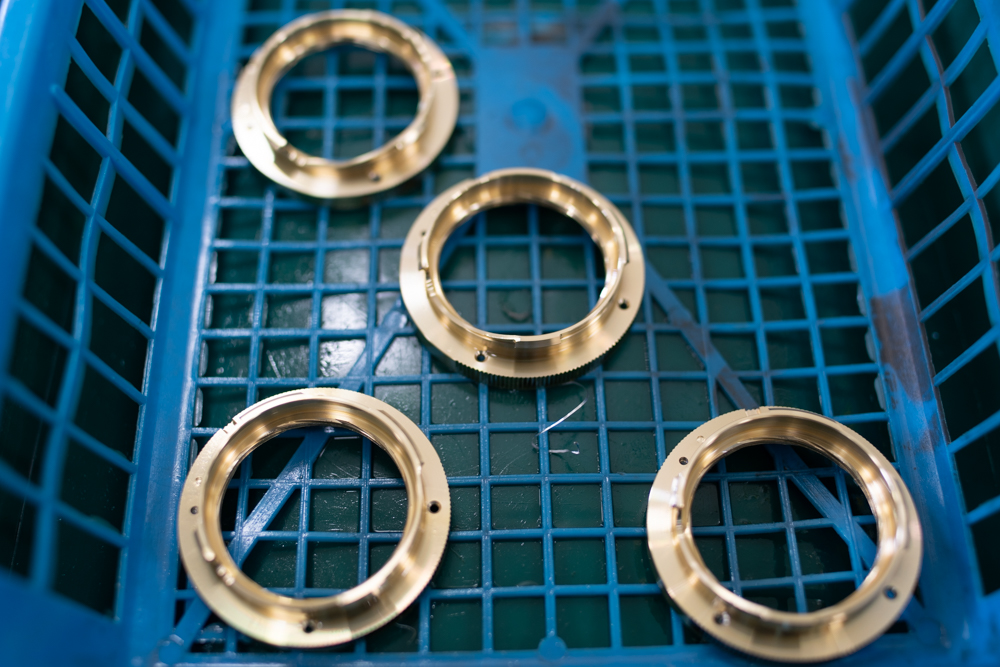
加工を終えたマウントパーツ。外側のバヨネットに加え、内側に内径リードネジが彫られているのがわかるだろう。
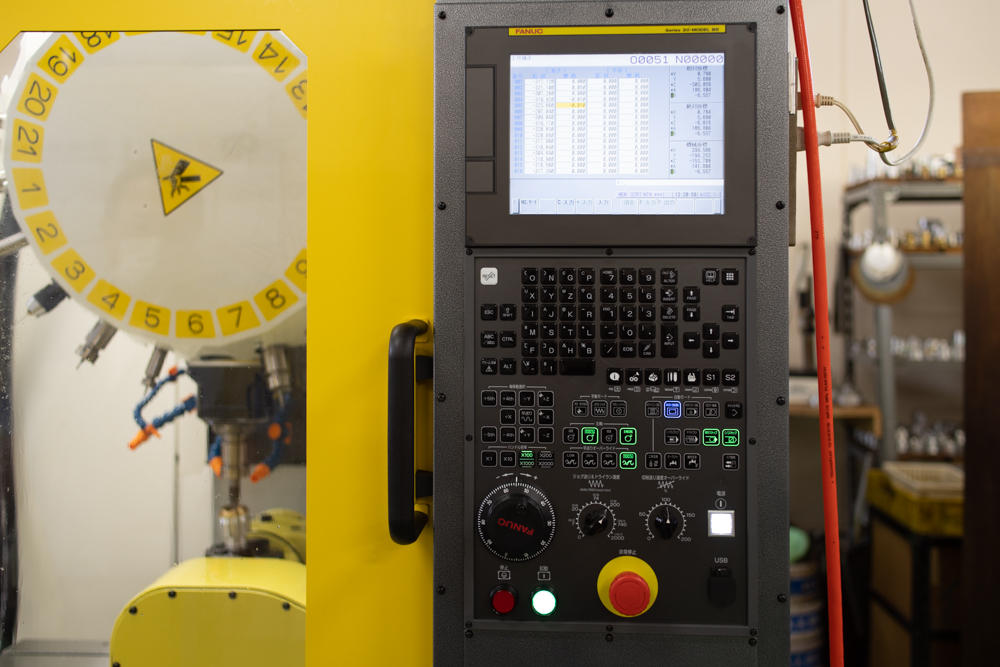
5軸マシニングセンタの動作はプログラムによって制御されている。加工中は無人でかまわないという。
5軸マシニングセンタは高精度な金属加工に欠かせない加工機だ。元となる金属塊の1面を固定し、固定面以外の5面まとめて加工できる。加工面ごとに固定し直す必要がないため、高精度に仕上げられるわけだ。加工工程はプログラムで指定し、もちろんここにも技術力が介在する。関口製作所はカメラやレンズを得意とする企業で、最近はシネレンズやシネカメラ、マシンビジョンレンズなどを手がけているという。文字通り、その道のプロフェッショナルである。
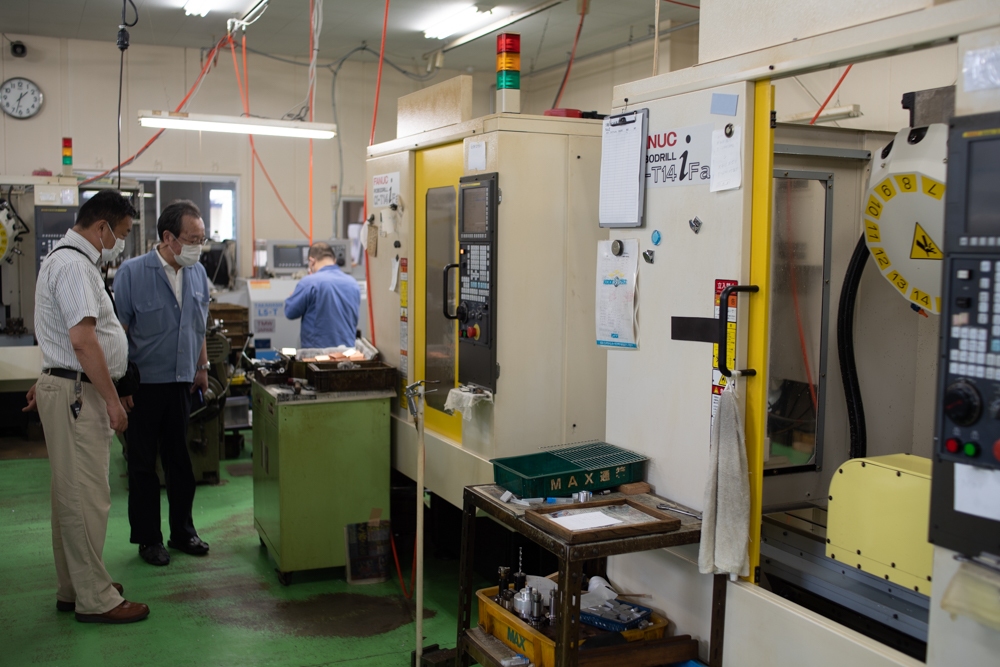
関口製作所では複数の5軸マシニングセンタが稼働し、様々な金属パーツを削り出していた。
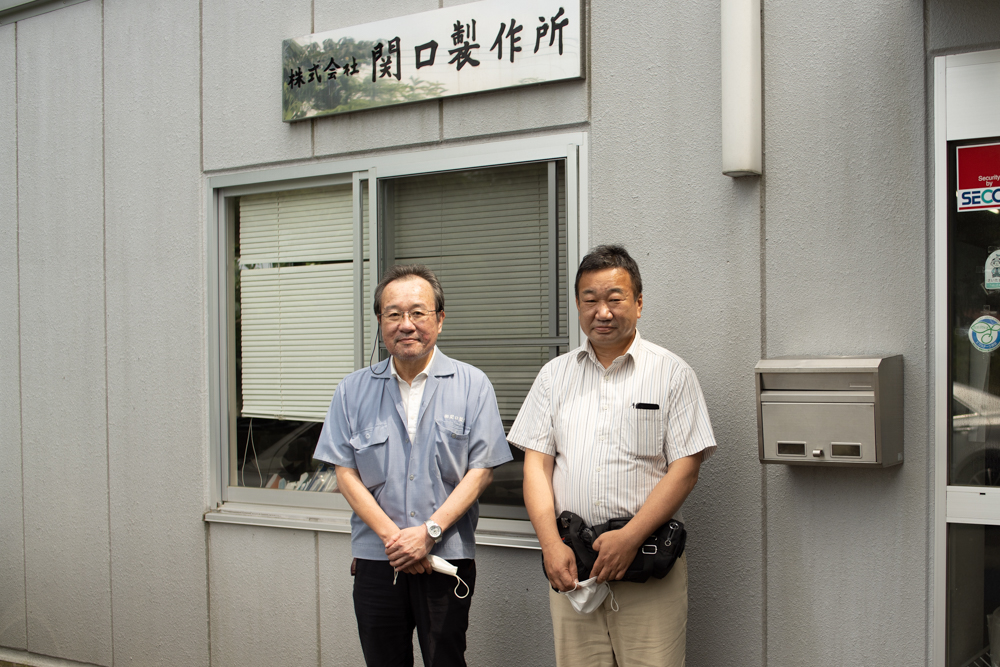
左が関口製作所代表の関口栄一氏、右が木下光学研究所代表の木下勉氏。ジャパンクオリティーとは彼らのような人たちに支えられているのだ。
今回、加工を見せてもらったマウントパーツは、距離計連動を担う大切な部品だ。試作用のパーツとはいえ、Mマウント版Kistar 40mm F2.4が製品化に向けて大きく前進したことを意味する。完成したレンズで実写できる日が待ち遠しい。(取材写真はKistar 35mm F1.4で撮影)。
Kistar 40mm F2.4
Kistarシリーズ4本目となるパンケーキレンズです。ミラーレス機に直接装着できるように、KSEマウントとKFXマウントを採用しました。レンズ構成は3群4枚のテッサー型。開放F2.4とやや明るめに設計することで、オールドレンズテイストの甘い開放描写を実現しています。現在、Mマウント版を計画中。